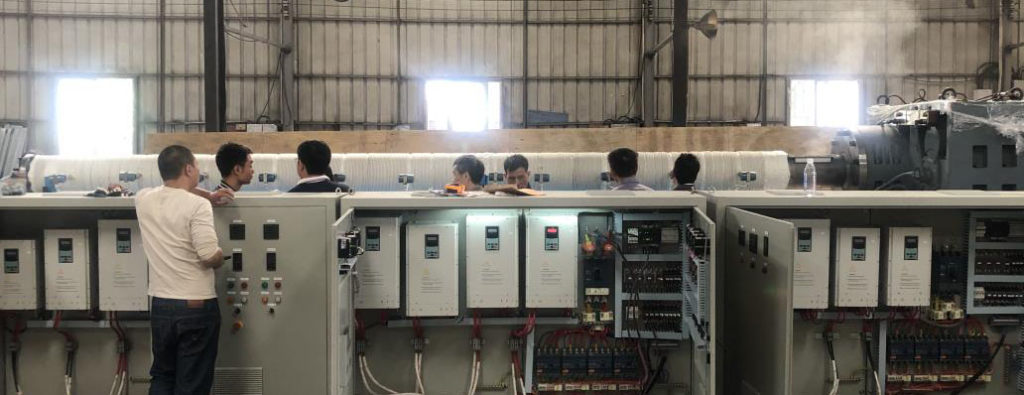
- Induction heating faster and higher effecient than resistance wire heating. Due to their different heating method, resistance wire mainly for heat itself and transfer thermal to plastic barral,huge thermal released on the air and waste thermal, time. Induction working on the plastic barral directly by the magnetic fields eddy.
- Induction has faster reaction on the heating speed on heating control. Induction power ouput easier get control than resistance wire heating. Induction can be control by 0-10V, 4-20 mA nalog control output power and in fast reaction on the heat speed. all online heat data could disply on the screen by RS485 or PLC.
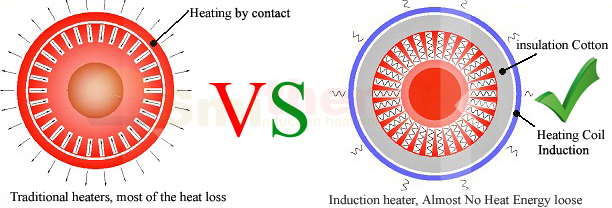
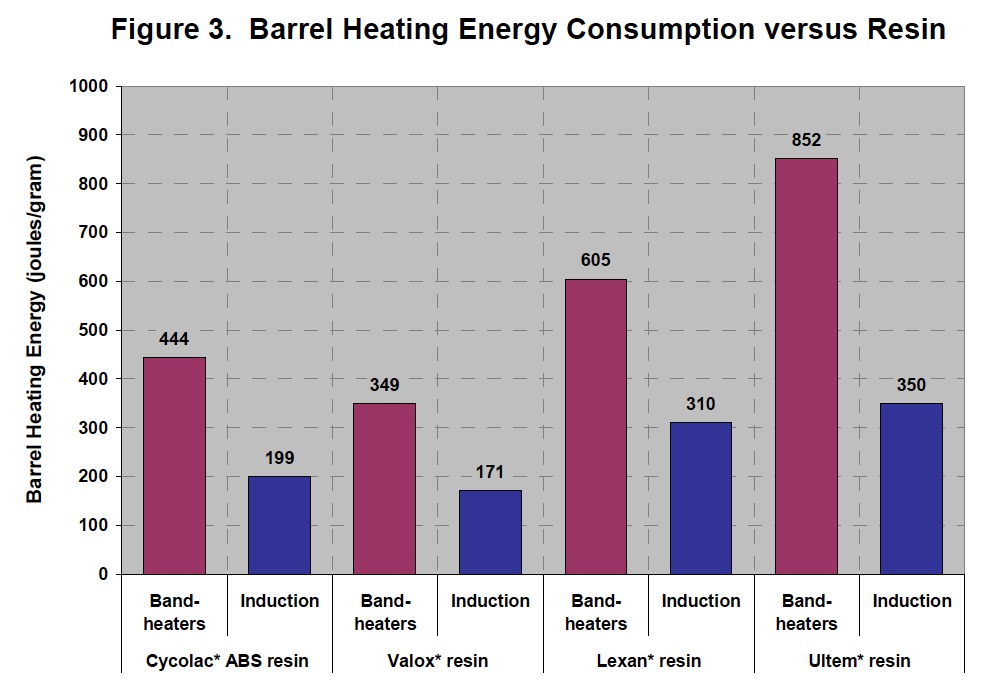
-
After customer replacement new induction heating and got display, same related power KW induction and resistance and consume electric energy consumption. Induction Power heating produce plastic pellet has 40%-50% higher production than resistance wire heating on same Power consume.
-
The heating element of Electromagnetic induction heater is copper coil cable with surface High temperature resistant to 500 degrees Celsius high temperature mica production, it has long working service. Not like as resistance wire after long time high temperature. it will ageing and shorter working time.
-
Insulation cotton made of fiberglass working as insulation and remain thermal for reduce thermal released to environment, keep max induction thermal to the plastic barral metal and working on the plastic pellet and granule processing and increase production.
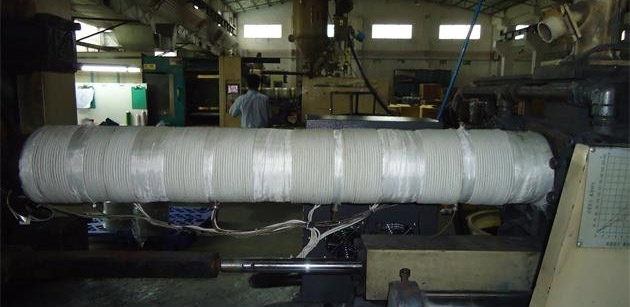

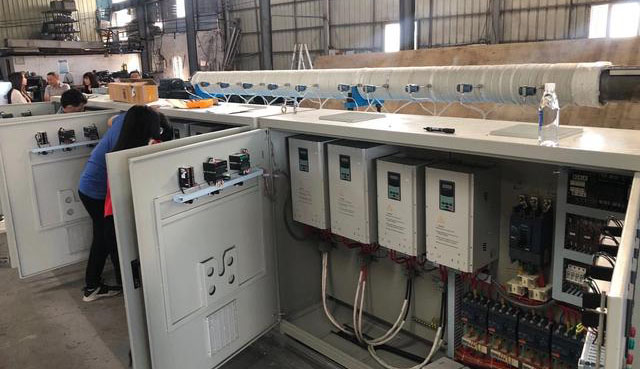
Why can electromagnetic heaters be efficient and stable?
- 1. During the cable coil winding process, sensitivity test and temperature distribution test should be carried out to ensure high sensitivity matching, to ensure its uniformity and high efficiency.
- 2. The internal control circuit is designed with an anti-interference circuit, which solves the problem of parallel interference of each coil and further improves the uniform stability.
- 3. The temperature control system in the external control circuit can accurately measure the temperature, and then control the non-polar power equipment through digital or analog signals, which ensures the heating efficiency and uniformity to a certain extent.
- 4. As we all know, in the heating process, a large part of the heat is lost to the air, resulting in high ambient temperature in the workshop and poor working conditions. When electromagnetic heating is applied, the heat insulation material is wrapped on the surface of the carrier to reduce heat loss. It can be used effectively, with high efficiency, and the production environment has also been improved to a certain extent.
- 5. The principle of electromagnetic heating is to use high-frequency alternating magnetic fields to make the carriers themselves do not need to conduct heat. The heating speed is fast and the efficiency is high. After testing, each kilowatt of electricity can generate 845 calories, and the thermal efficiency is as high as 98.7%.
- 6. The internal circuit is a series resonant circuit, which will perform a series of rectification and filtering processes on the current to ensure the output waveform is clean and stable, thereby ensuring stability.
Where do we need electromagnetic induction heater application ?